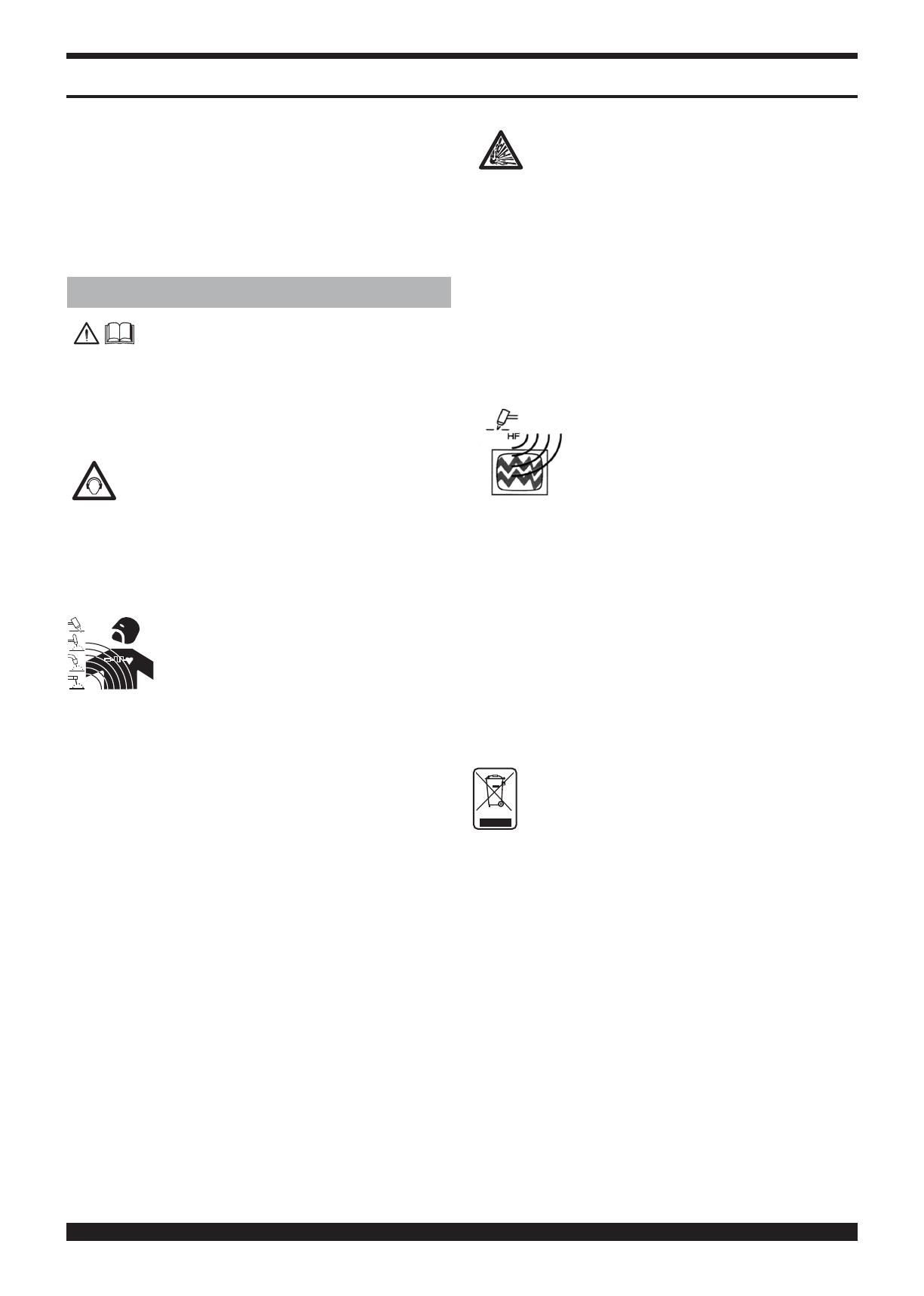
18
BEDIENUNGSANLEITUNG FÜR LICHTBOGENSCHWEISSMASCHINEN
WICHTIG: VOR DER INBETRIEBNAHME DES GERÄTS
DEN INHALT DER VORLIEGENDEN BETRIEBSANLEI-
TUNG AUFMERKSAM DURCHLESEN; DIE BETRIEBS-
ANLEITUNG MUSS FÜR DIE GESAMTE LEBENSDAUER
DES GERÄTS AN EINEM ALLEN INTERESSIERTEN PER-
SONEN BEKANNTEN ORT AUFBEWAHRT WERDEN.
DIESES GERÄT DARF AUSSCHLIESSLICH ZUR AUS-
FÜHR- UNG VON SCHWEISSARBEITEN VERWENDET
WERDEN.
1 SICHERHEITSVORSCHRIFTEN
DAS LICHTBOGENSCHWEISSEN UND
SCHNEIDEN KANN FÜR SIE UND ANDERE
GESUNDHEITSSCHÄDLICH SEIN; daher muß der Be-
nutzer über die nachstehend kurz dargelegten Gefahren
beim Schweißen unterrichtet werden. Für ausführlichere
Informationen das Handbuch Nr. 3.300758 anfordern.
LÄRM
Dieses Gerät erzeugt selbst keine Geräusche, die
80 dB überschreiten. Beim Plasmaschneid- und
Plasmaschweißprozeß kann es zu einer Geräu-
schentwicklung kommen, die diesen Wert überschreitet.
Daher müssen die Benutzer die gesetzlich vorgeschrie-
benen Vorsichtsmaßnahmen treffen.
ELEKTROMAGNETISCHE FELDER - Schädlich können
sein:
· Der elektrische Strom, der durch einen be-
liebigenLeiterießt,erzeugtelektromagne-
tische Felder (EMF). Der Schweiß- oder
Schneidstrom erzeugt elektromagnetische
Felder um die Kabel und die Stromquellen.
• Die durch große Ströme erzeugten magnetischen Felder
können den Betrieb von Herzschrittmachern stören. Trä-
ger von lebenswichtigen elektronischen Geräten (Herz-
schrittmacher) müssen daher ihren Arzt befragen, bevor
sie sich in die Nähe von Lichtbogenschweiß-, Schneid-,
Brennputz- oder Punktschweißprozessen begeben.
• Die Aussetzung an die beim Schweißen oder Schnei-
den erzeugten elektromagnetischen Felder kann bislang
unbekannte Auswirkungen auf die Gesundheit haben.
Um die Risiken durch die Aussetzung an elektromagne-
tische Felder zu mindern, müssen sich alle SchweißerIn-
nen an die folgenden Verfahrensweisen halten:
- Sicherstellen, dass das Massekabel und das Kabel
der Elektrodenzange oder des Brenners nebeneinan
der bleiben. Die Kabel nach Möglichkeit mit einem
Klebeband aneinander befestigen.
- Das Massekabel und das Kabel der
Elektrodenzange oder des Brenners nicht um den
Körper wickeln.
- Sich nicht zwischen das Massekabel und das Kabel
der Elektrodenzange oder des Brenners stellen.
Wenn sich das Massekabel rechts vom Schweißer
bzw.derSchweißerinbendet,musssichauchdas
Kabel der Elektrodenzange oder des Brenners auf
dieserSeitebenden.
- Das Massekabel so nahe wie möglich an der
Schweiß- oder Schneidstelle an das Werkstück
anschließen.
- Nicht in der Nähe der Stromquelle arbeiten.
EXPLOSIONSGEFAHR
· Keine Schneid-/Schweißarbeiten in der Nähe
von Druckbehältern oder in Umgebungen aus-
führen, die explosiven Staub, Gas oder Dämpfe
enthalten. Die für den Schweiß-/Schneiprozeß verwen-
detenGasaschenundDruckreglersorgsambehandeln.
ELEKTROMAGNETISCHE VERTRÄGLICHKEIT
Dieses Gerät wurde in Übereinstimmung mit den Angaben
der harmonisierten Norm IEC 60974-10 (Cl. A) konstruiert
und darf ausschließlich zu gewerblichen Zwecken und nur
in industriellen Arbeitsumgebungen verwendet werden. Es
ist nämlich unter Umständen mit Schwierigkeiten verbunden
ist, die elektromagnetische Verträglichkeit des Geräts in an-
deren als industriellen Umgebungen zu gewährleisten.
HOCHFREQUENZ (HF)
• Die Hochfrequenz (HF) kann die Funkna-
vigation, Sicherheitsdienste, Computer
und allgemein Kommunikationsgeräte stö-
ren.
• Die Installation darf nur von Fachkräften
ausgeführt werden, die mit elektronischen
Geräten vertraut sind.
• Es fällt in die Verantwortung des Endbenutzers, sich
einesqualiziertenElektrotechnikerszubedienen,derje-
des durch die Installation verursachte Störungsproblem
prompt beheben kann.
• Wenn von der FCC eine Mitteilung wegen Störungen
ergeht, ist der Betrieb des Geräts unverzüglich einzustel-
len.
• Das Gerät muss regelmäßig kontrolliert und gewartet
werden.
• Der Hochfrequenzgenerator darf nicht geöffnet wer-
den. Darauf achten, dass die Elektroden der Funkenstre-
cke den richtigen Abstand haben.
ENTSORGUNG DER ELEKTRO- UND ELEKTRO-
NIKGERÄTE
Elektrogeräte dürfen niemals gemeinsam mit ge-
wöhnlichenAbfällenentsorgtwerden!InÜberein-
stimmung mit der Europäischen Richtlinie 2002/96/EG
über Elektro- und Elektronik-Altgeräte und der jeweili-
gen Umsetzung in nationales Recht sind nicht mehr ver-
wendete Elektrogeräte gesondert zu sammeln und einer
Anlage für umweltgerechtes Recycling zuzuführen. Als
Eigentümer der Geräte müssen Sie sich bei unserem ört-
lichen Vertreter über die zugelassenen Sammlungssyste-
me informieren. Die Umsetzung genannter Europäischer Richt-
liniewirdUmweltundmenschlicherGesundheitzugutekommen!
IM FALLE VON FEHLFUNKTIONEN MUSS MAN SICH AN
EINEN FACHMANN WENDEN.
1.1 WARNHINWEISSCHILD
Die Nummerierung der Beschreibungen entspricht der
Nummerierung der Felder des Schilds.
B. Die Drahtförderrollen können Verletzungen an den
Händen verursachen.
C. Der Schweißdraht und das Drahtvorschubgerät ste-
hen während des Schweißens unter Spannung. Die
Hände und Metallgegenstände fern halten.