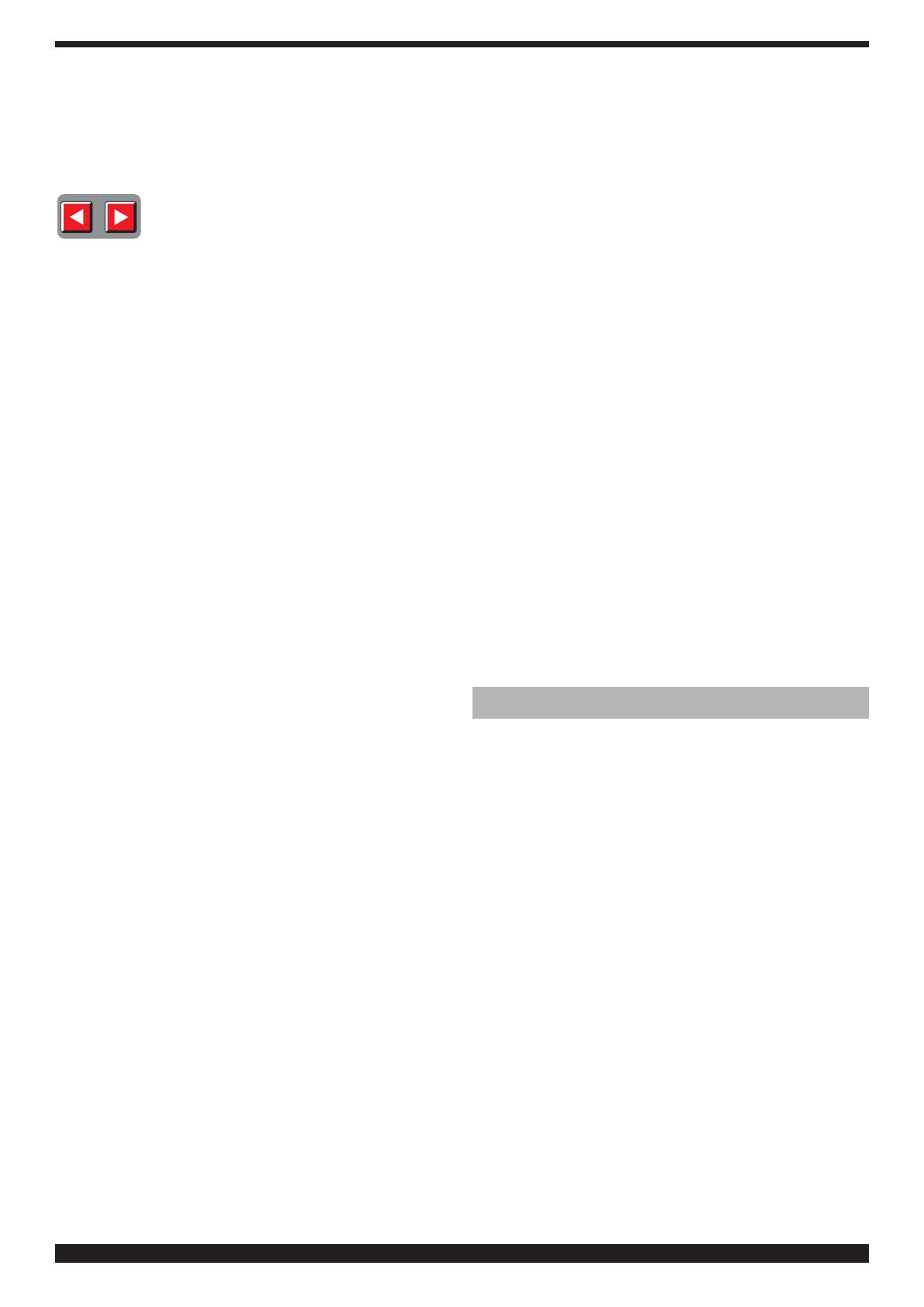
13
speed. If you wish to correct this speed, simply turn
the knob clockwise to increase or counter-clockwise to
decrease. Changes in wire speed are always indicated on
the display S by a current.
Q and R- Keys.
• When the LED B is lit, the display S shows
the program number selected by the 2 keys.
Once the selection has been completed the
LED remains lit for 5 more seconds, then shuts off.
• When the LED C is lit the display S shows the time
selected by the 2 keys. Once the selection has been
completed the LED remains lit for 5 more seconds, then
shuts off.
• When the LED D is lit, the display S shows the time
selected by the 2 keys. Once the selection has been
completed the LED remains lit for 5 more seconds, then
shuts off.
• When the LED E is lit the display S shows the time
selected by the 2 keys. Once the selection has been
completed the LED remains lit for 5 more seconds, then
shuts off.
• When the LEDs B, C, D, and E are off and we are within
any synergic program, pressing one of the 2 keys will
cause the display S to show either the current set or the
recommended thickness in millimeters.
Adjusting the 2 selector switches N and O allows you
to immediately see, on the display S, the increase or
decrease in the value selected. This function is used
when one wishes to know in advance at what current or
thickness welding is to begin.
• Pressing the 2 keys simultaneously for at least 5
seconds causes us to enter the sub-menu, where we
nd3functionsthatmaybeselectedviathekeyA:
1- Soft Start (speed).
Changes the wire speed from the one set; this speed
remains active for the time governed by the Soft Start
function (time).
The speed may be adjusted using the 2 keys Q and R from
10% to a maximum of 150% of the set welding speed.
This function, combined with the Soft Start function (time),
serves to improve arc striking. The value shown on the
display S is preceded by the letter (A).
2- Speed set on the motor of the PULL 2003.
Adjusting the two keys Q and R varies the speed of the
PULL 2003 from –9 to +9 compared to the set value. This
function maximizes wire advancement, putting the wire
feeder motor of the welding machine in step with the
motor of the PULL 2003. The value shown on the display
S is preceded by the letter (H).
3- Post gas.
Using the two keys Q and R, it is possible to adjust the
gas ow after welding to between 0 and 5 seconds.
This function is especially useful when welding stainless
steel and aluminum. The value shown on the display S is
preceded by the letter (P).
4- Soft Start (time).
Adjusts the time for which the Soft Start speed remains
active. This function, combined with the Soft Start function
(speed), serves to improve arc striking.
Using the 2 keys Q and R, the Soft Start time may be
adjusted from 0 to 1 second. The value shown on the
display S is preceded by the letter (d).
5- Two-stage manual mode and 4-stage automatic
mode.
Adjust the 2 keys Q and R to select the 2-stage or 4-stage
mode.
If the welding machine is set to 2-stage manual mode,
welding begins when the button E is pressed, and stops
when it is released.
If the welding machine is set to 4-stage automatic mode,
press the torch trigger to begin welding; you may release
the trigger once the procedure has begun.
Press and release the trigger again to stop welding. This
setting is suitable for long-term welding, where the welder
may tire of holding down the torch trigger. The value
shown on the display S is preceded by the symbols (2T
and 4T).
S- Display.
Using the manual program 00 the instrument displays the
wire speed in meters per minute before welding, and the
current while welding.
Using the synergic programs it always displays the
current.
As described in the paragraphs above, the following may
be displayed on the instrument before beginning to weld:
the program being used, the spot welding time, the pause
time, the Burn-Back time, the recommended thickness,
the Soft Start function, the speed set on the motor of the
PULL 2003, and the post-gas time.
5 WELDING
5.1 Installation
Make sure that the wire diameter corresponds to the
diameter indicated on the wire feeder roller, and that the
selected program is compatible with the material and type
ofgas.Usewirefeederrollerswitha“U”-shapedgroove
for aluminum wires, and with a “V”-shaped groove for
other wires.
5.2 THE MACHINE IS READY TO WELD
When using the Pull-2003 or Spool-Gun torch, follow
the instructions enclosed.
• Connect the earth clamp to the workpiece.
• Set the switch to 1.
• Remove the gas nozzle.
• Unscrew the contact tip.
• Insert the wire in the wire liner of the torch, making sure
that it is inside the roller groove and that the roller is in the
correct position.
• Press the torch trigger to move the wire forward until it
comes out of the torch.
• Caution: keep your face away from the gun tube
assembly while the wire is coming out.
• Screw the contact tip back on, making sure that the hole
diameter is the same as that of the wire used.
• Assemble the gas nozzle.
5.3 WELDING CARBON STEELS WITHOUT GAS