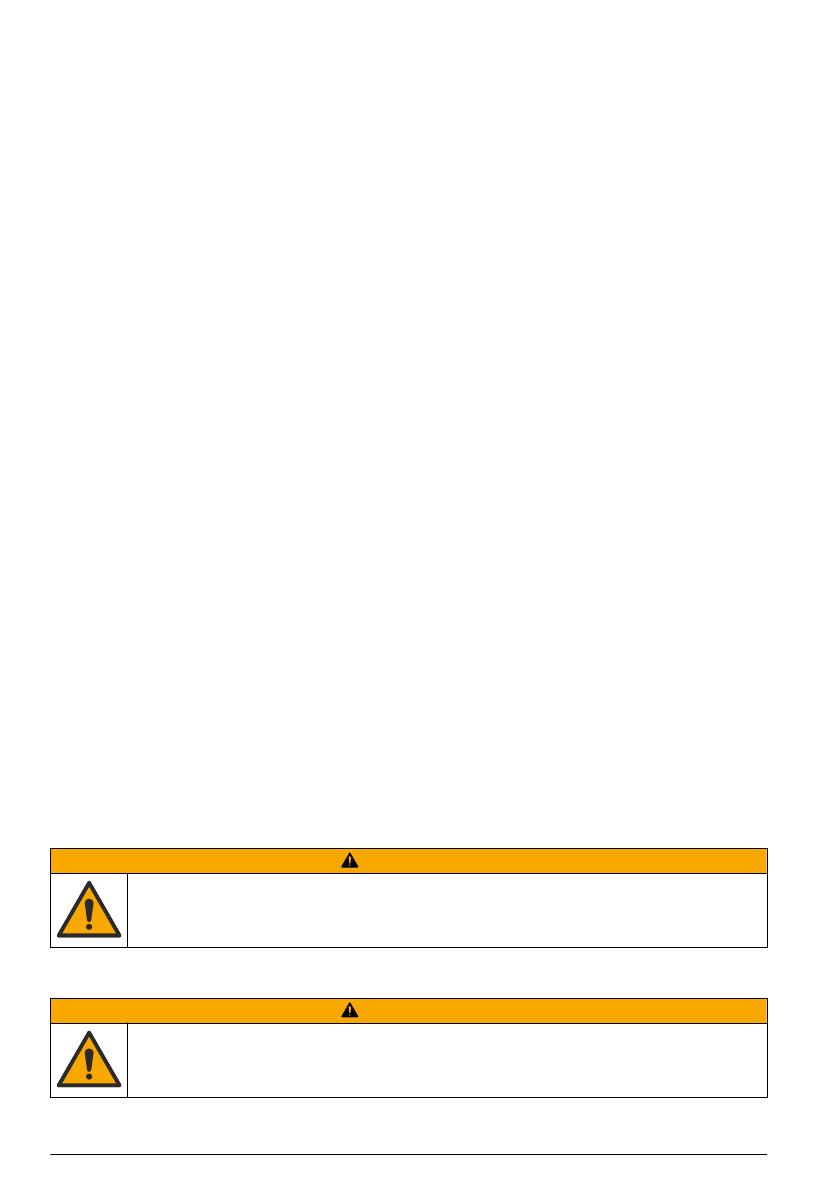
A plastic screw-on base is also provided to protect the connection socket, and which also provides a
suitable stand for the sensor during maintenance procedures, and when not in use.
4.2.2 Protection caps
Non-ATEX sensors (GA2400)
Two protection caps will be delivered with each sensor, one without a grille (part number 33051-S0)
and one with a grille (part number 33051-SP).
A third protection cap (part number 33051-SG) is also available as an option and improves the
maintenance interval for beer or soft drinks process applications.
A fourth protection cap (part number 33051-ST) is delivered for the 6110 TPA application.
ATEX sensors (GA2800)
Only one protection cap will be delivered with each sensor (part number 33051-SG or 33051-H0).
4.2.3 Sensor recharge kit
A recharge kit should have been ordered with the sensor as this will be required to initially make the
sensor operational. It is also required for sensor cleaning and membrane replacement procedures.
Note: There are two different versions of the recharge kit. One version for GA2X00/A110X sensors and one version
for C1100 sensors. Refer to the documentation supplied with the kit for instructions on how to use the version of the
recharge kit with the applicable sensor.
The kit contains:
• four recharge cartridges with pre-mounted membrane and electrolyte. The type of membrane
mounted in the cartridge will be specific to the kit ordered
• two anode cleaning tools
• two sets of five cotton washers and five silicone discs (only for 2956A-XXX)
Note: The box for GA2X00 sensors has a blue label and the box for A110X sensors has a black label.
• one set of replacement O-rings and Dacron
®
mesh patches, applicable for GA2X00 and A110X
sensors
The blue anode cleaning tool is used to clean the anode of any deposits or residue that may have
formed. It is doubled-ended so it can be used for two membrane replacement processes, each end
being used once. Refer to the documentattion supplied with the recharge kit for instructions on how
to use the anode cleaning tool for a GA2X00 sensor or for a A110X sensor.
The cotton washers provide additional protection against the formation of deposits and residue on
the center electrode and anode, which prolongs the time period required between sensor
maintenance.
The silicone discs are required for measurements in ultra-pure water or water containing ammonia.
The Dacron
®
mesh patches provide protection to the membrane when using a protection cap with a
grille.
Section 5 Installation
C A U T I O N
Multiple hazards. Only qualified personnel must conduct the tasks described in this section of the
document.
5.1 Sensor preparation
C A U T I O N
Chemical exposure hazard. Obey laboratory safety procedures and wear all of the personal
protective equipment appropriate to the chemicals that are handled. Refer to the current safety data
sheets (MSDS/SDS) for safety protocols.
8 English